Projektübersicht
1. Produktionsprogramm
600 Sätze/Tag (117/118 Lagerböcke)
2. Anforderungen an die Verarbeitungslinie:
1) NC-Bearbeitungszentrum, geeignet für automatische Produktionslinien;
2) Hydraulische Kittelklemme;
3) Automatische Lade- und Stanzvorrichtung und Fördervorrichtung;
4) Allgemeine Verarbeitungstechnologie und Verarbeitungszykluszeit;
Layout der Produktionslinien
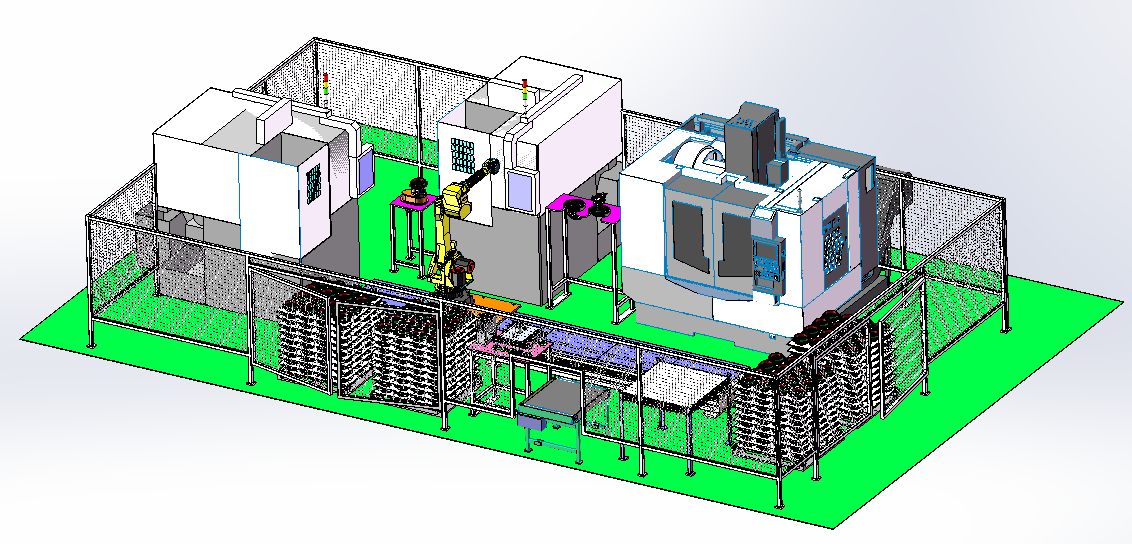
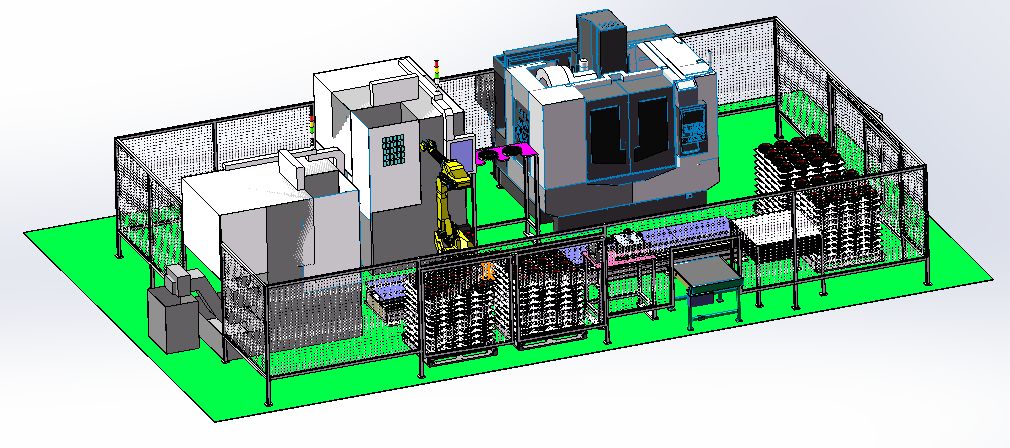
Layout der Produktionslinien
Einführung von Roboteraktionen:
1. Die grob bearbeiteten und platzierten Körbe manuell auf den Ladetisch (Ladetische Nr. 1 und Nr. 2) legen und mit der Taste bestätigen;
2. Der Roboter bewegt sich zum Tablett des Ladetisches Nr. 1, öffnet das Sichtsystem, greift die Teile A und B und bewegt sie jeweils zur Winkelanzeigestation, um auf die Ladeanweisung zu warten.
3. Die Ladeanweisung wird von der Winkelerkennungsstation gesendet. Der Roboter legt Teil Nr. 1 in den Positionierungsbereich des Drehtellers. Drehen Sie den Drehteller und starten Sie das Winkelerkennungssystem. Bestimmen Sie die Winkelposition, stoppen Sie den Drehteller und beenden Sie die Winkelerkennung von Teil Nr. 1.
4. Das Winkelerkennungssystem sendet den Befehl zum Ausschneiden. Der Roboter nimmt das Teil Nr. 1 auf und legt das Teil Nr. 2 zur Identifizierung ein. Der Drehtisch dreht sich, und das Winkelerkennungssystem startet, um die Winkelposition zu bestimmen. Der Drehtisch stoppt, und die Winkelerkennung von Teil Nr. 2 ist abgeschlossen. Anschließend wird der Befehl zum Ausschneiden gesendet.
5. Der Roboter empfängt den Stanzbefehl der Vertikaldrehmaschine Nr. 1 und fährt zur Lade- und Stanzposition der Vertikaldrehmaschine Nr. 1, um das Material auszuschneiden und zu laden. Nach Abschluss dieser Aktion beginnt der Einzelteilbearbeitungszyklus der Vertikaldrehmaschine.
6. Der Roboter nimmt die fertigen Produkte von der Vertikaldrehbank Nr. 1 und platziert sie an Position Nr. 1 auf dem Werkstück-Überrolltisch.
7. Der Roboter empfängt den Stanzbefehl der Vertikaldrehmaschine Nr. 2, bewegt sich zur Lade- und Stanzposition der Vertikaldrehmaschine Nr. 2, um das Material auszuschneiden und zu laden. Anschließend ist der Vorgang abgeschlossen und der Einzelteilverarbeitungszyklus der Vertikaldrehmaschine beginnt.
8. Der Roboter nimmt die fertigen Produkte von der Vertikaldrehbank Nr. 2 und platziert sie an Position Nr. 2 auf dem Werkstück-Überrolltisch.
9. Der Roboter wartet auf den Ausschneidebefehl von der vertikalen Bearbeitung.
10. Die Vertikalbearbeitung sendet den Stanzbefehl, und der Roboter fährt zur Lade- und Stanzposition der Vertikalbearbeitung, greift die Werkstücke der Stationen Nr. 1 und Nr. 2 und befördert sie jeweils zum Stanztablett und legt sie jeweils darauf ab. Der Roboter fährt zum Überrolltisch, um die Teile Nr. 1 und Nr. 2 zu greifen und an die Lade- und Stanzpositionen der Vertikalbearbeitung zu befördern, und legt die Werkstücke Nr. 1 und Nr. 2 jeweils in den Positionierungsbereich der Stationen Nr. 1 und Nr. 2 der hydraulischen Klemme, um die Vertikalbearbeitung abzuschließen. Der Roboter fährt aus dem Sicherheitsabstand der Vertikalbearbeitung heraus und startet einen einzelnen Bearbeitungszyklus.
11. Der Roboter bewegt sich zum Ladefach Nr. 1 und bereitet den Start des sekundären Zyklusprogramms vor.
Beschreibung:
1. Der Roboter nimmt 16 Teile (eine Lage) auf das Ladefach. Der Roboter ersetzt die Saugnapfzange und legt die Trennplatte in den Zwischenlagerkorb.
2. Der Roboter packt 16 Teile (eine Schicht) auf das Stanztablett. Der Roboter sollte die Saugnapfzange einmal austauschen und die Trennplatte auf die Trennfläche der Teile aus dem temporären Lagerkorb legen.
3. Stellen Sie entsprechend der Inspektionsfrequenz sicher, dass der Roboter ein Teil auf den manuellen Probenahmetisch legt.
1 | Der Zeitplan für den Bearbeitungszyklus | ||||||||||||||
2 | Kunde | Werkstückstoff | QT450-10-GB/T1348 | Modell der Werkzeugmaschine | Archivnummer | ||||||||||
3 | Produktname | 117 Lagersitz | Zeichnungsnr. | DZ90129320117 | Datum der Erstellung | 04.01.2020 | Hergestellt von | ||||||||
4 | Prozessschritt | Messer Nr. | Bearbeitungsinhalt | Werkzeugname | Schnittdurchmesser | Schnittgeschwindigkeit | Drehzahl | Vorschub pro Umdrehung | Vorschub durch Werkzeugmaschine | Anzahl der Stecklinge | Jeder Prozess | Bearbeitungszeit | Leerlaufzeit | Vierachsige Rotationszeit | Werkzeugwechselzeit |
5 | NEIN. | NEIN. | Beschreibungen | Werkzeuge | D mm | n | R Uhr | mm/U | mm/Min | Mal | mm | Sek | Sek | Sek | |
6 | ![]() | ||||||||||||||
7 | 1 | T01 | Fräsen der Befestigungslochoberfläche | Durchmesser des 40-Scheibenfräsers | 40,00 | 180 | 1433 | 1,00 | 1433 | 8 | 40,0 | 13.40 | 8 | 4 | |
8 | Bohren Sie DIA 17 Befestigungslöcher | DIA 17 KOMBINIERTER BOHRER | 17.00 | 100 | 1873 | 0,25 | 468 | 8 | 32,0 | 32,80 | 8 | 4 | |||
9 | T03 | DIA 17 Lochrückwandabschrägung | Rückwärtsfasfräser | 16.00 | 150 | 2986 | 0,30 | 896 | 8 | 30,0 | 16.08 | 16 | 4 | ||
10 | Beschreibung: | Schnittzeit: | 62 | Zweite | Zeit zum Spannen mit der Vorrichtung und zum Laden und Stanzen von Materialien: | 30.00 | Zweite | ||||||||
11 | Nebenzeit: | 44 | Zweite | Gesamtbearbeitungsstunden: | 136,27 | Zweite |
1 | Der Zeitplan für den Bearbeitungszyklus | |||||||||||||||||
2 | Kunde | Werkstückstoff | QT450-10-GB/T1348 | Modell der Werkzeugmaschine | Archivnummer | |||||||||||||
3 | Produktname | 118 Lagersitz | Zeichnungsnr. | DZ90129320118 | Datum der Erstellung | 04.01.2020 | Hergestellt von | |||||||||||
4 | Prozessschritt | Messer Nr. | Bearbeitungsinhalt | Werkzeugname | Schnittdurchmesser | Schnittgeschwindigkeit | Drehzahl | Vorschub pro Umdrehung | Vorschub durch Werkzeugmaschine | Anzahl der Stecklinge | Jeder Prozess | Bearbeitungszeit | Leerlaufzeit | Vierachsige Rotationszeit | Werkzeugwechselzeit | |||
5 | NEIN. | NEIN. | Beschreibungen | Werkzeuge | D mm | n | R Uhr | mm/U | mm/Min | Mal | mm | Sek | Sek | Sek | ||||
6 | ![]() | |||||||||||||||||
7 | 1 | T01 | Fräsen der Befestigungslochoberfläche | Durchmesser des 40-Scheibenfräsers | 40,00 | 180 | 1433 | 1,00 | 1433 | 8 | 40,0 | 13.40 | 8 | 4 | ||||
8 | T02 | Bohren Sie DIA 17 Befestigungslöcher | DIA 17 KOMBINIERTER BOHRER | 17.00 | 100 | 1873 | 0,25 | 468 | 8 | 32,0 | 32,80 | 8 | 4 | |||||
9 | T03 | DIA 17 Lochrückwandabschrägung | Rückwärtsfasfräser | 16.00 | 150 | 2986 | 0,30 | 896 | 8 | 30,0 | 16.08 | 16 | 4 | |||||
10 | Beschreibung: | Schnittzeit: | 62 | Zweite | Zeit zum Spannen mit der Vorrichtung und zum Laden und Stanzen von Materialien: | 30.00 | Zweite | |||||||||||
11 | Nebenzeit: | 44 | Zweite | Gesamtbearbeitungsstunden: | 136,27 | Zweite | ||||||||||||
12 |
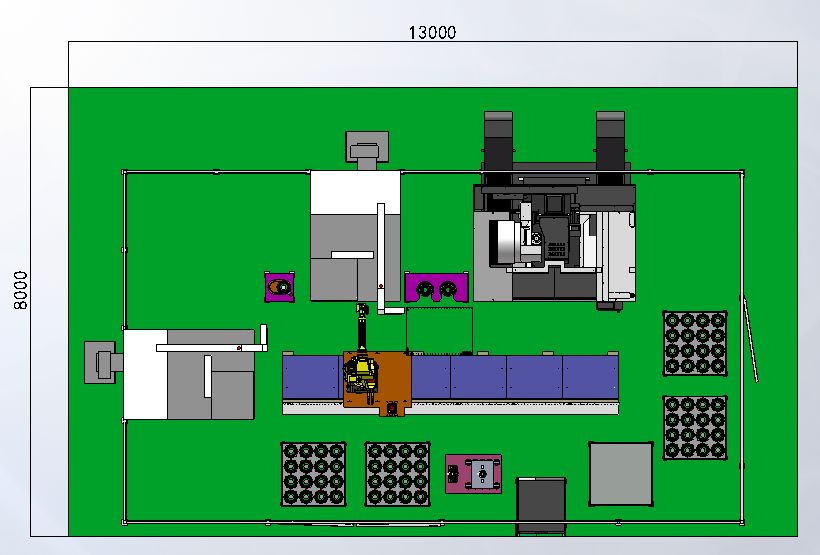
Abdeckungsbereich der Produktionslinie
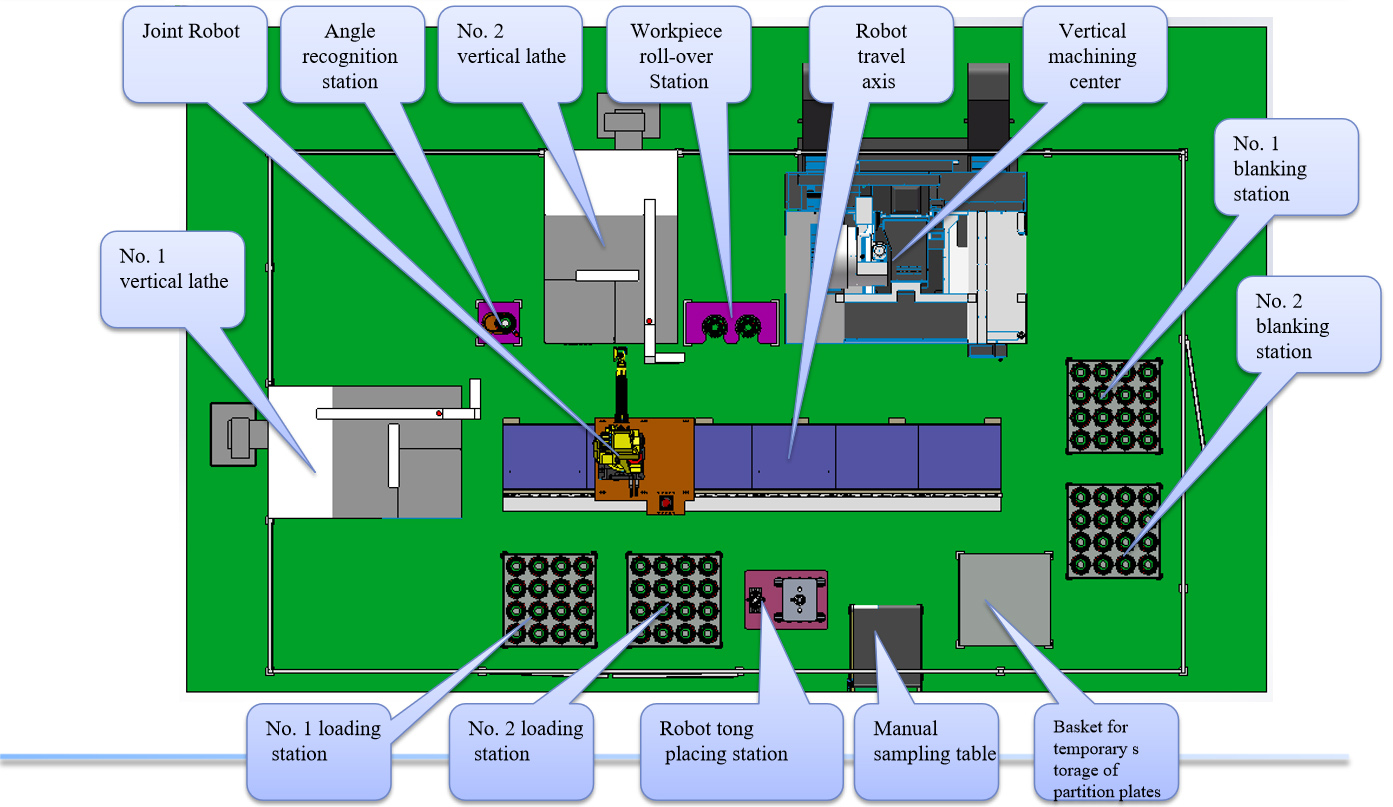
Einführung der wichtigsten Funktionskomponenten der Produktionslinie
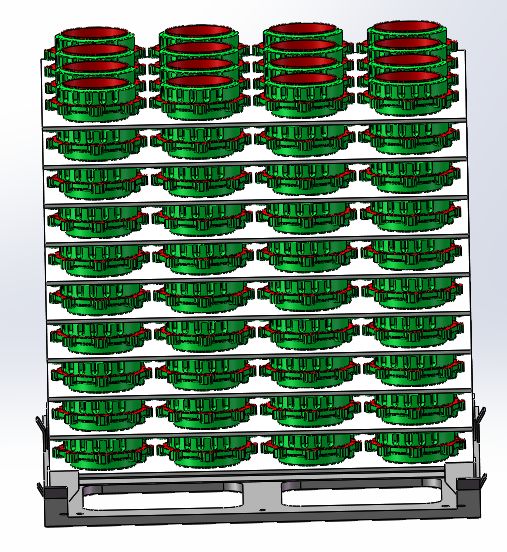
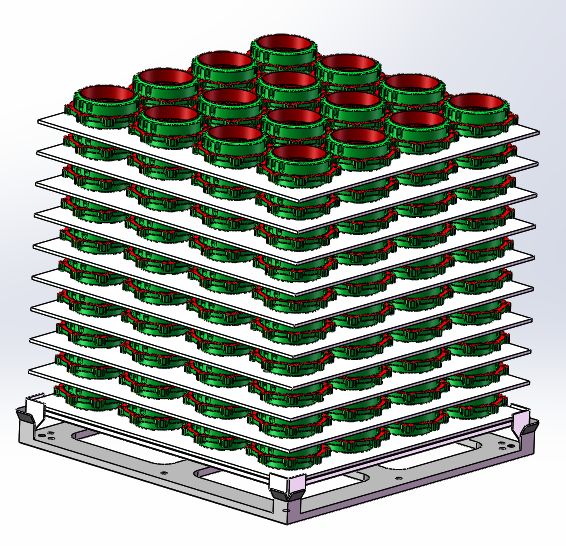
Einführung des Lade- und Zuschnittsystems
Die Lagerausrüstung für die automatische Produktionslinie in diesem Schema besteht aus: dem gestapelten Tablett (die Anzahl der auf jedes Tablett zu packenden Teile wird mit dem Kunden ausgehandelt) und der Positionierung des Werkstücks im Tablett wird nach Bereitstellung einer 3D-Zeichnung des Werkstückrohlings oder des tatsächlichen Objekts bestimmt.
1. Die Arbeiter packen die grob bearbeiteten Teile auf die Materialablage (wie in der Abbildung gezeigt) und heben sie mit dem Gabelstapler an die vorgesehene Position.
2. Nachdem Sie die Ablage des Gabelstaplers wieder eingesetzt haben, drücken Sie zur Bestätigung manuell die Taste.
3. Der Roboter greift das Werkstück, um die Ladearbeit auszuführen;
Einführung der Roboter-Fahrachse
Die Struktur besteht aus einem Gelenkroboter, einem Servomotorantrieb und einem Ritzel- und Zahnstangenantrieb, sodass der Roboter geradlinige Hin- und Herbewegungen ausführen kann. Sie verwirklicht die Funktion eines Roboters, der mehrere Werkzeugmaschinen bedient und Werkstücke an mehreren Stationen greift, und kann den Arbeitsbereich von Gelenkrobotern erhöhen.
Die Fahrschiene weist eine aus Stahlrohren geschweißte Basis auf und wird durch einen Servomotor, ein Ritzel und einen Zahnstangenantrieb angetrieben, um den Arbeitsbereich des Gelenkroboters zu vergrößern und die Auslastung des Roboters effektiv zu verbessern. Die Fahrschiene wird auf dem Boden installiert.
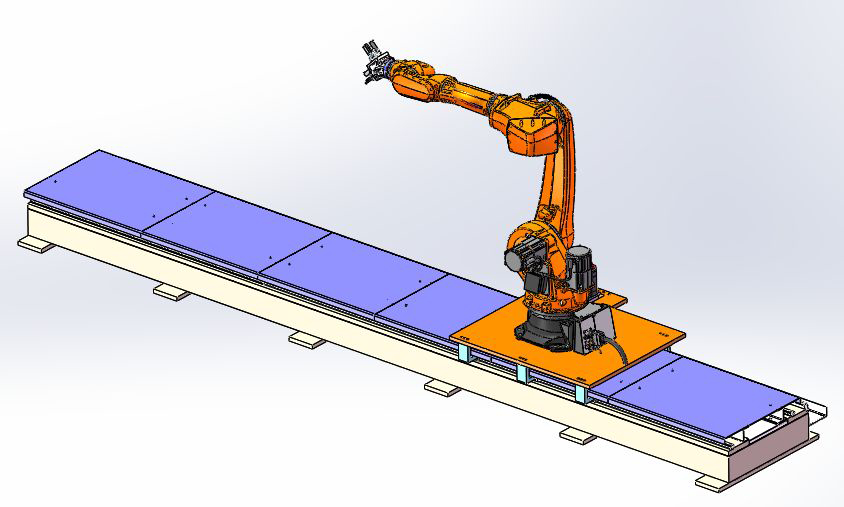
Chenxuan-Roboter: SDCX-RB500
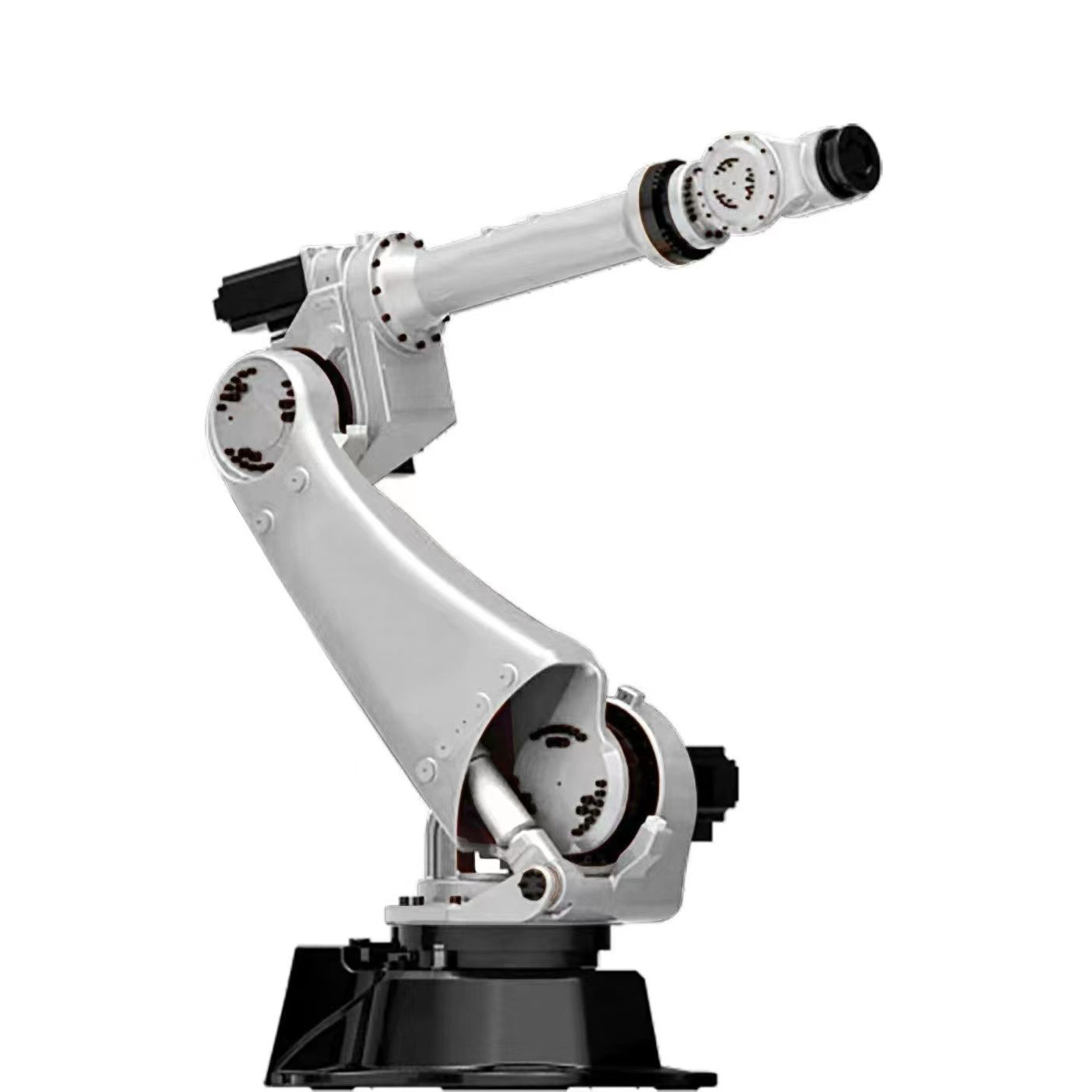
Basisdaten | |
Typ | SDCX-RB500 |
Anzahl der Achsen | 6 |
Maximale Abdeckung | 2101 mm |
Posenwiederholbarkeit (ISO 9283) | ±0,05 mm |
Gewicht | 553 kg |
Schutzklassifizierung des Roboters | Schutzart IP65 / IP67Inline-Handgelenk(IEC 60529) |
Einbaulage | Decke, zulässiger Neigungswinkel ≤ 0º |
Oberflächenbehandlung, Lackierung | Grundrahmen: schwarz (RAL 9005) |
Umgebungstemperatur | |
Betrieb | 283 K bis 328 K (0 °C bis +55 °C) |
Lagerung und Transport | 233 K bis 333 K (-40 °C bis +60 °C) |
Dank des großen Bewegungsbereichs an der Rückseite und Unterseite des Roboters kann das Modell an der Decke montiert werden. Da die seitliche Breite des Roboters auf das Maximum reduziert ist, kann er dicht am benachbarten Roboter, an der Klemme oder am Werkstück installiert werden. Schnelle Bewegung von der Standby-Position in die Arbeitsposition und schnelle Positionierung bei Kurzstreckenbewegungen.
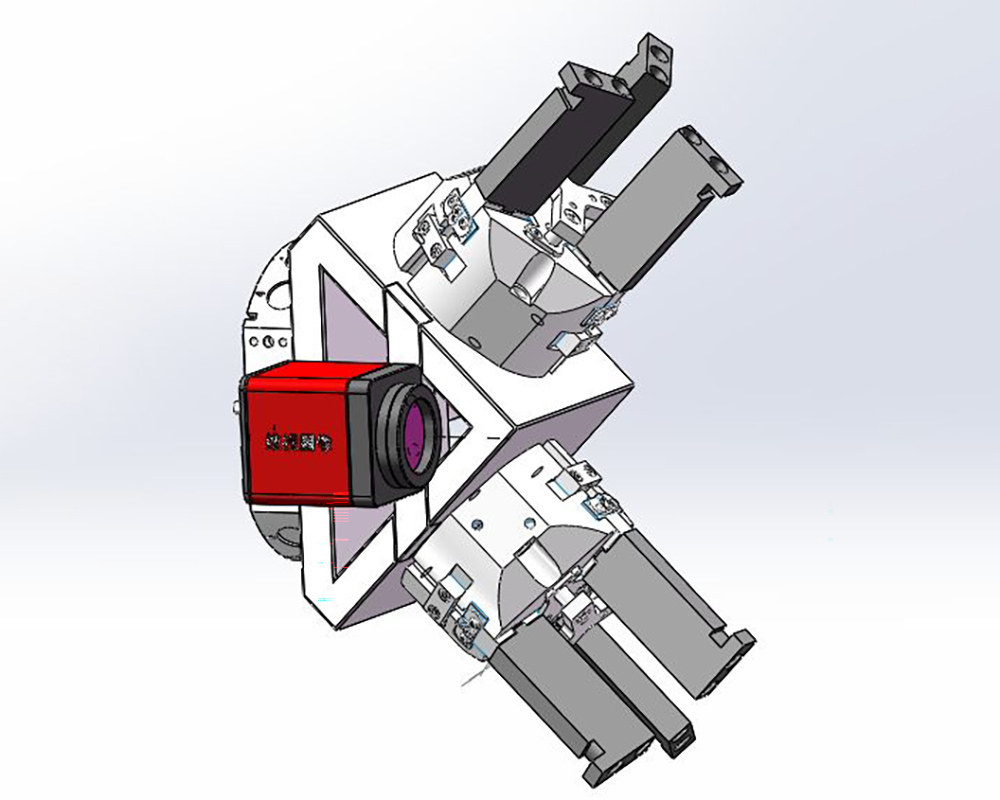
Intelligenter Roboterlade- und Stanzzangenmechanismus
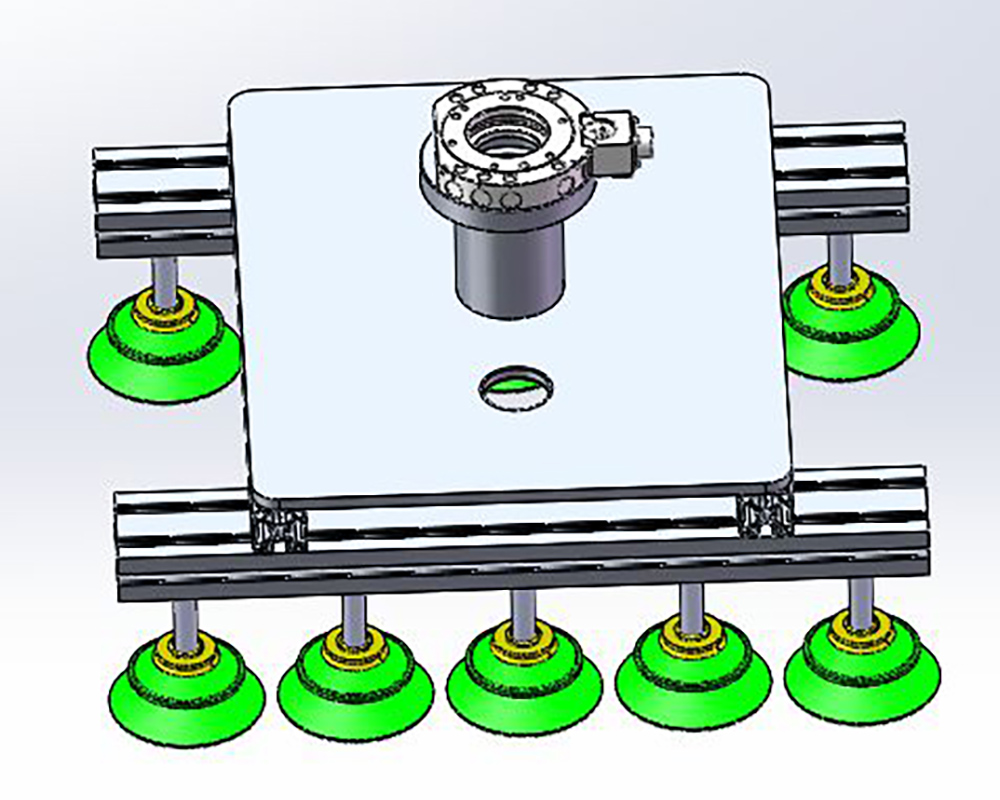
Roboter-Trennplatten-Zangenmechanismus
Beschreibung:
1. In Anbetracht der Eigenschaften dieses Teils verwenden wir zum Laden und Stanzen der Materialien die externe Stützmethode mit drei Klauen, wodurch ein schnelles Drehen der Teile in der Werkzeugmaschine ermöglicht wird.
2. Der Mechanismus ist mit einem Positionserkennungssensor und einem Drucksensor ausgestattet, um festzustellen, ob der Klemmzustand und der Druck der Teile normal sind.
3. Der Mechanismus ist mit einem Druckhalter ausgestattet, und das Werkstück fällt bei einem Stromausfall und einer Gasunterbrechung des Hauptluftkreislaufs nicht innerhalb kurzer Zeit ab.
4. Handwechselvorrichtung wird übernommen. Der Wechselzangenmechanismus kann das Spannen verschiedener Materialien schnell abschließen.
Einführung der Zangenwechselvorrichtung
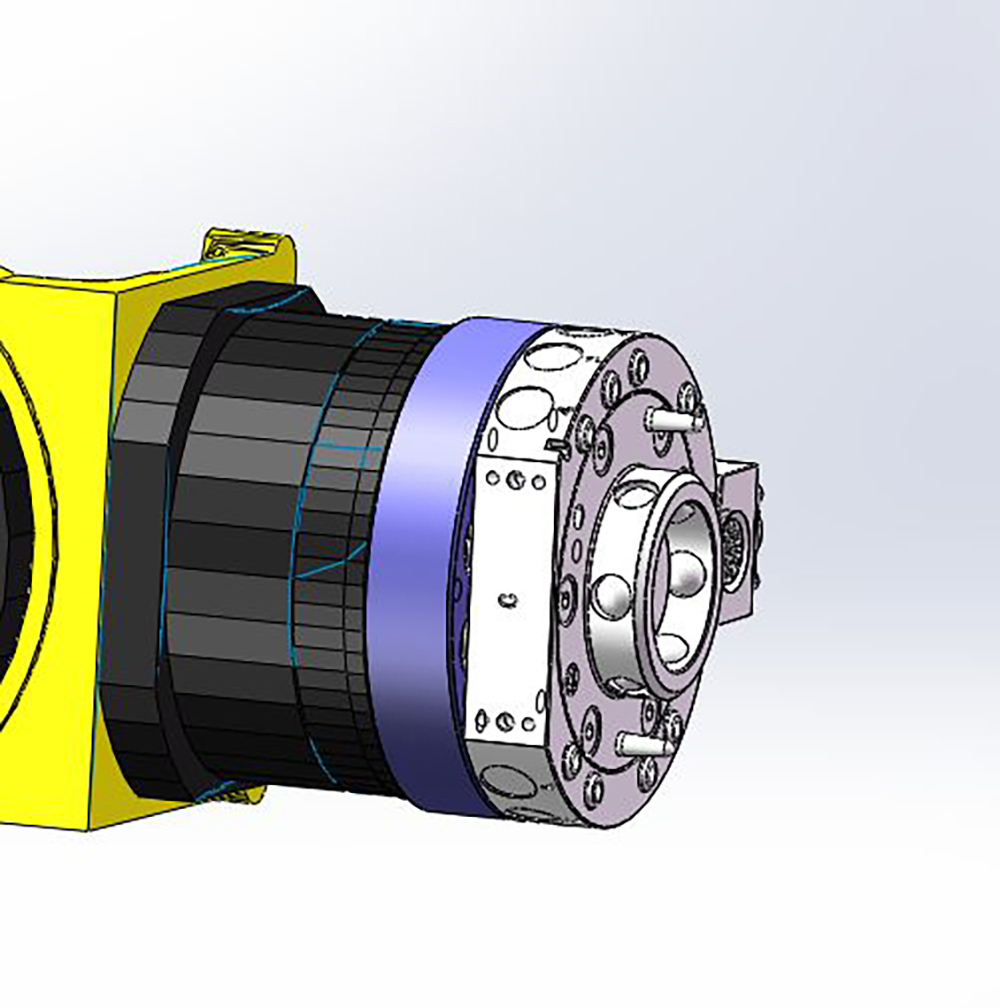
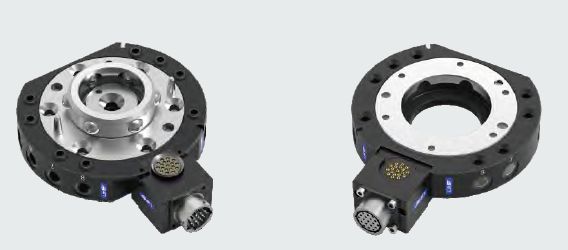
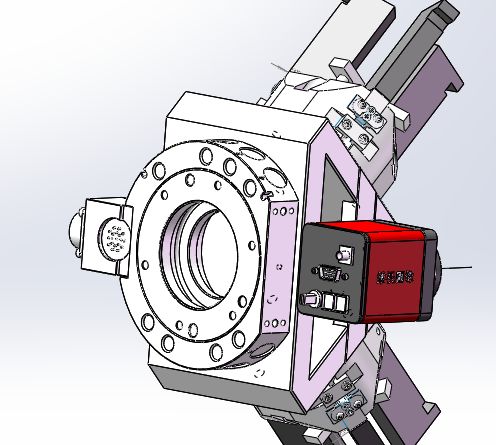
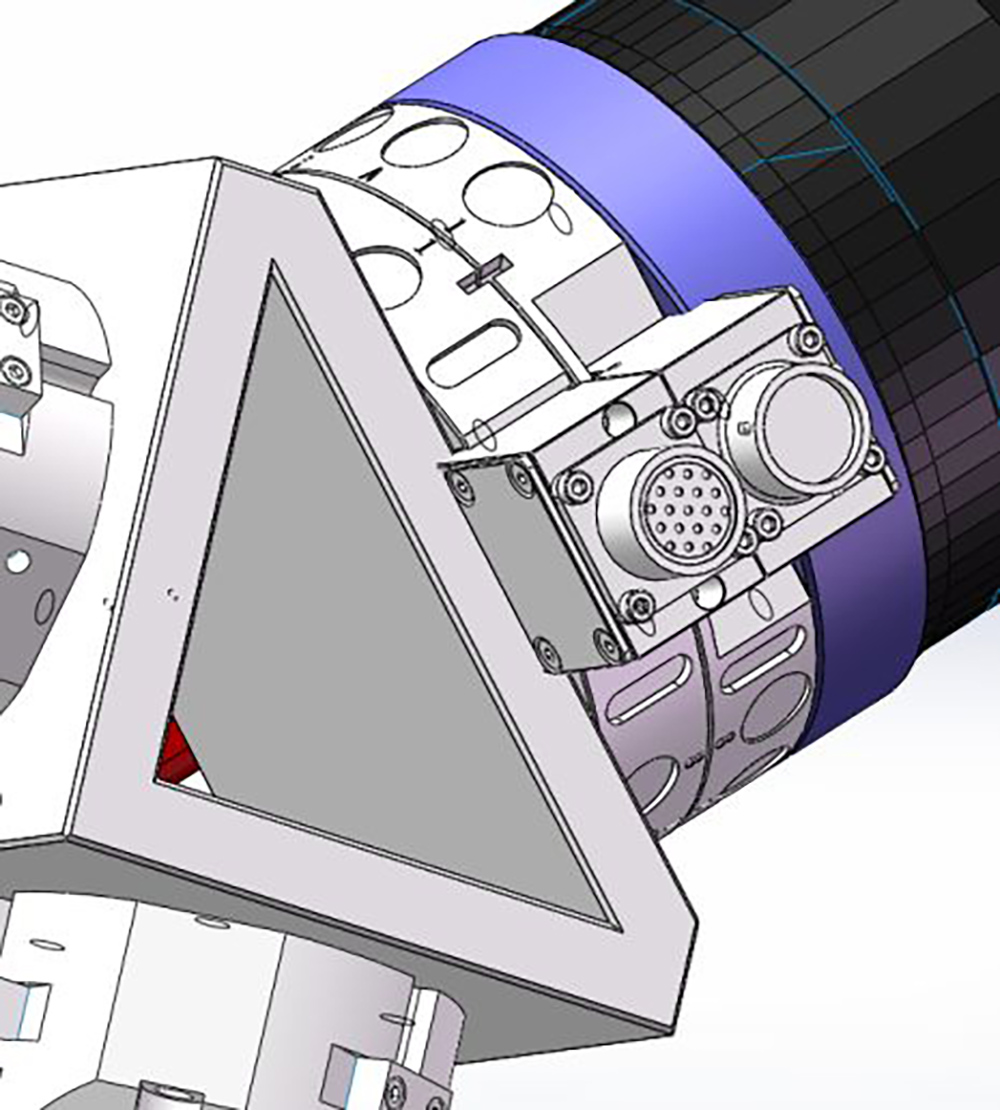
Präzise Zangenwechselvorrichtungen ermöglichen den schnellen Wechsel von Roboterzangen, Werkzeugenden und anderen Aktuatoren. Reduzieren Sie Produktionsleerzeiten und erhöhen Sie die Roboterflexibilität.
1. Luftdruck entriegeln und festziehen;
2. Es können verschiedene Strom-, Flüssigkeits- und Gasmodule verwendet werden.
3. Die Standardkonfiguration ermöglicht eine schnelle Verbindung mit der Luftquelle.
4. Spezielle Versicherungsagenturen können das Risiko einer versehentlichen Gasabschaltung verhindern.
5. Keine Federreaktionskraft; 6. Anwendbar im Automatisierungsbereich;
Einführung in Vision System-Industriekamera
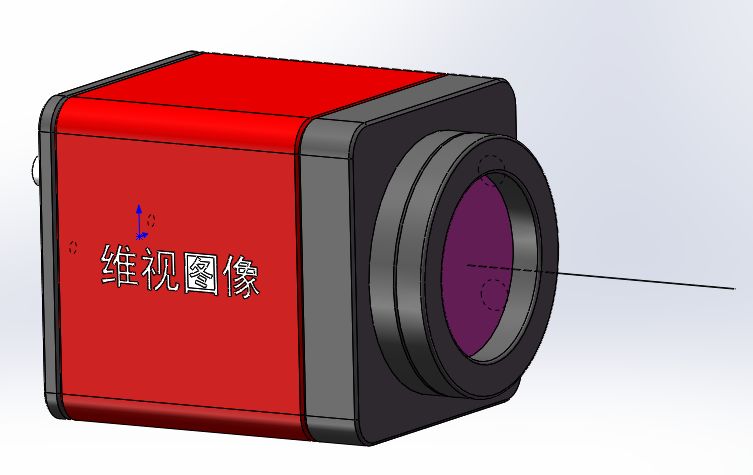
1. Die Kamera verwendet hochwertige CCD- und CMDS-Chips, die sich durch ein hohes Auflösungsverhältnis, hohe Empfindlichkeit, ein hohes Signal-Frequenz-Verhältnis, einen großen Dynamikbereich, eine hervorragende Bildqualität und eine erstklassige Farbwiederherstellung auszeichnen.
2. Die Area-Array-Kamera verfügt über zwei Datenübertragungsmodi: Gigabit-Ethernet-Schnittstelle (GigE) und USB3.0-Schnittstelle;
3. Die Kamera hat eine kompakte Struktur, ist klein, leicht und installiert. Hohe Übertragungsgeschwindigkeit, starke Entstörungsfähigkeit, stabile Ausgabe von Bildern in hoher Qualität; Es ist anwendbar zum Lesen von Codes, zur Fehlererkennung, DCR und Mustererkennung; Die Farbkamera verfügt über eine starke Farbwiederherstellungsfähigkeit und eignet sich für Szenarien mit hohen Anforderungen an die Farberkennung.
Einführung des automatischen Erkennungssystems Angular
Funktionseinführung
1. Der Roboter spannt die Werkstücke aus den Ladekörben und befördert sie in den Positionierungsbereich des Drehtisches;
2. Der Drehteller dreht sich unter dem Antrieb des Servomotors.
3. Das visuelle System (Industriekamera) dient zur Erkennung der Winkelposition und der Drehtisch stoppt, um die erforderliche Winkelposition zu bestimmen.
4. Der Roboter entnimmt das Werkstück und legt ein weiteres Stück zur Winkelerkennung hinein;
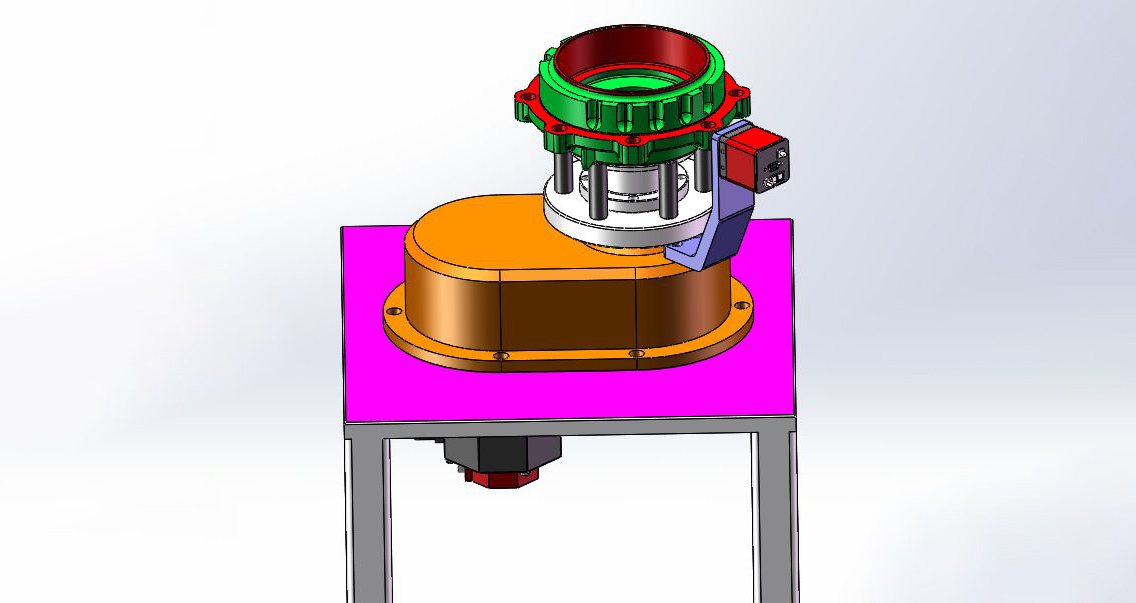
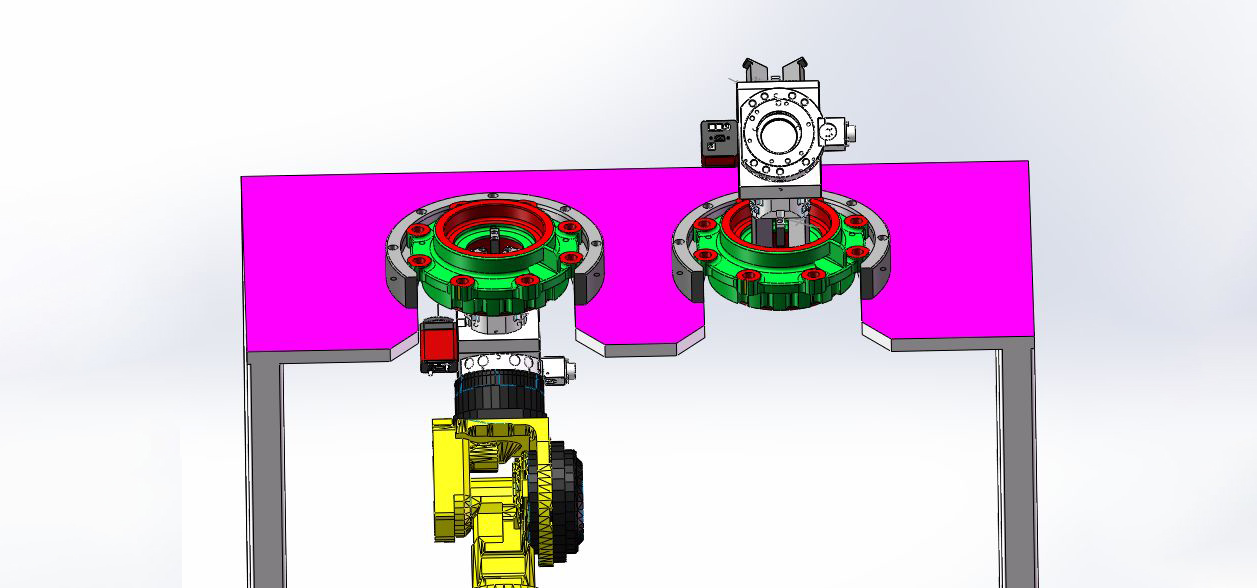
Einführung in den Werkstück-Überrolltisch
Überrollstation:
1. Der Roboter nimmt das Werkstück und legt es im Positionierungsbereich auf dem Rolltisch ab (die linke Station in der Abbildung).
2. Der Roboter greift das Werkstück von oben, um das Überrollen des Werkstücks zu realisieren.
Roboterzangen-Platzierungstisch
Funktionseinführung
1. Nachdem jede Teileschicht geladen wurde, muss die geschichtete Trennplatte in den Zwischenlagerkorb für die Trennplatten gelegt werden.
2. Der Roboter kann durch die Zangenwechselvorrichtung schnell durch Saugnapfzangen ersetzt und die Trennplatten entfernt werden.
3. Nachdem die Trennplatten richtig platziert sind, nehmen Sie die Saugnapfzange ab und ersetzen Sie sie durch die pneumatische Zange, um mit dem Laden und Stanzen der Materialien fortzufahren.
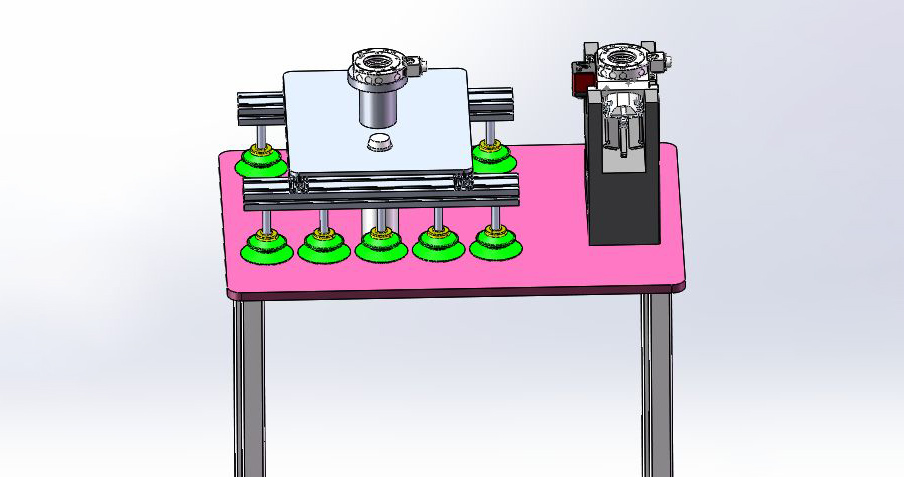
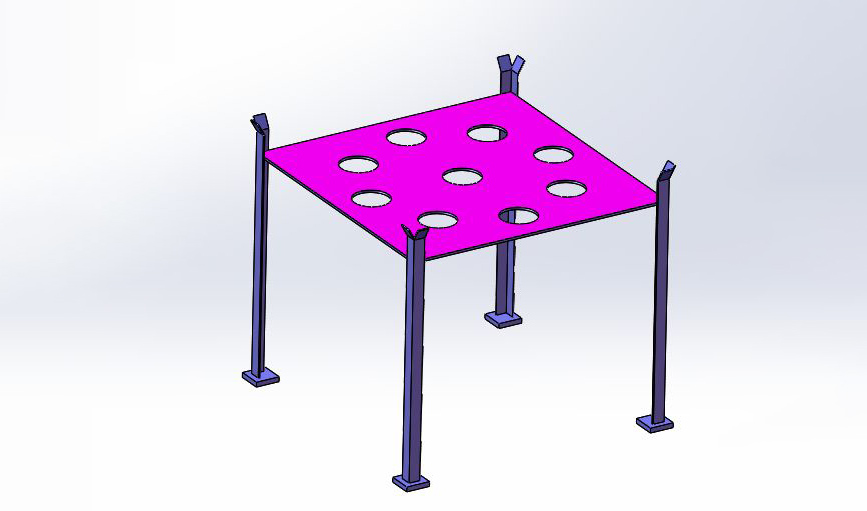
Korb zur Zwischenlagerung von Trennplatten
Funktionseinführung
1. Ein temporärer Korb für Trennplatten wird entworfen und geplant, da die Trennplatten zum Laden zuerst entnommen und die Trennplatten zum Stanzen später verwendet werden.
2. Die Ladetrennplatten werden manuell platziert und weisen eine schlechte Konsistenz auf. Nachdem die Trennplatte in den temporären Lagerkorb gelegt wurde, kann der Roboter sie herausnehmen und ordentlich platzieren.
Manueller Probenahmetisch
Beschreibung:
1. Legen Sie für verschiedene Produktionsphasen unterschiedliche manuelle Stichprobenfrequenzen fest, um die Wirksamkeit der Online-Messung effektiv zu überwachen.
2. Gebrauchsanweisung: Der Manipulator legt das Werkstück entsprechend der manuell eingestellten Frequenz an die eingestellte Position auf dem Probenahmetisch und weist mit dem roten Licht darauf hin. Der Prüfer drückt die Taste, um das Werkstück in den Sicherheitsbereich außerhalb des Schutzes zu transportieren, nimmt das Werkstück zur Messung heraus und lagert es nach der Messung separat.
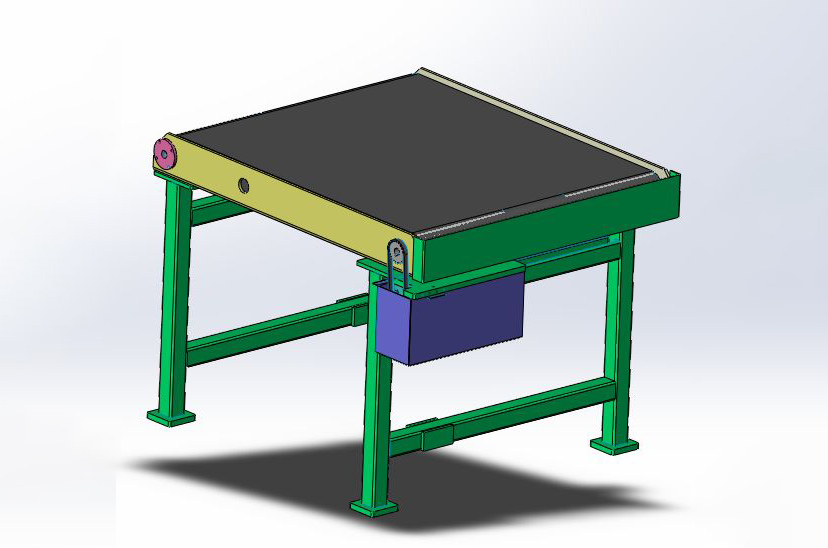
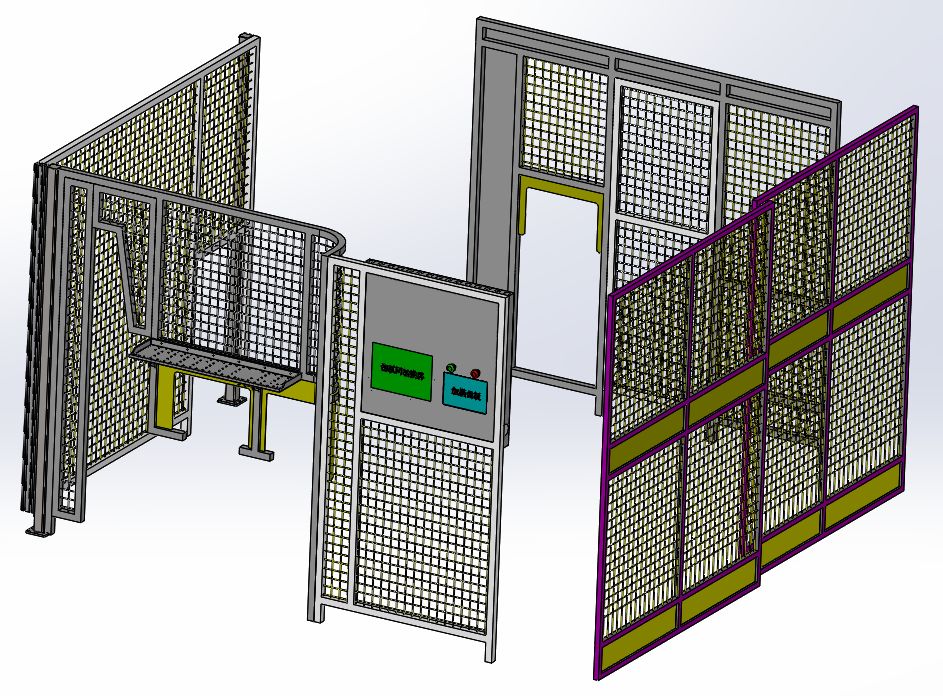
Schutzkomponenten
Es besteht aus einem leichten Aluminiumprofil (40×40) + Netz (50×50), und der Touchscreen und der Not-Aus-Schalter können in die Schutzkomponenten integriert werden, wodurch Sicherheit und Ästhetik vereint werden.
Einführung der hydraulischen Vorrichtung OP20
Verarbeitungshinweise:
1. Nehmen Sie die Innenbohrung mit φ165 als Basisloch, nehmen Sie den Bezugspunkt D als Basisebene und nehmen Sie den Außenbogen des Vorsprungs der beiden Montagelöcher als Winkelgrenze.
2. Steuern Sie den Löse- und Pressvorgang der Pressplatte durch den Befehl der Werkzeugmaschine M, um die Anfasbearbeitung der oberen Ebene des Montagelochvorsprungs, des 8-φ17-Montagelochs und beider Enden des Lochs abzuschließen.
3. Die Vorrichtung verfügt über die Funktionen Positionierung, automatisches Spannen, Luftdichtheitserkennung, automatisches Lösen, automatisches Auswerfen, automatisches Spanspülen und automatisches Reinigen der Positionierungsbezugsebene.
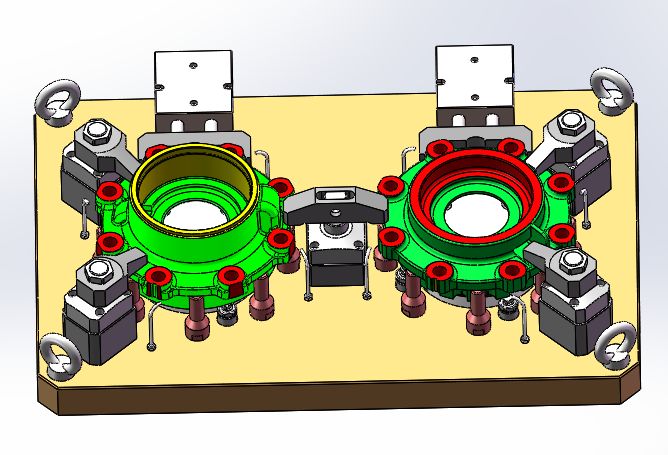
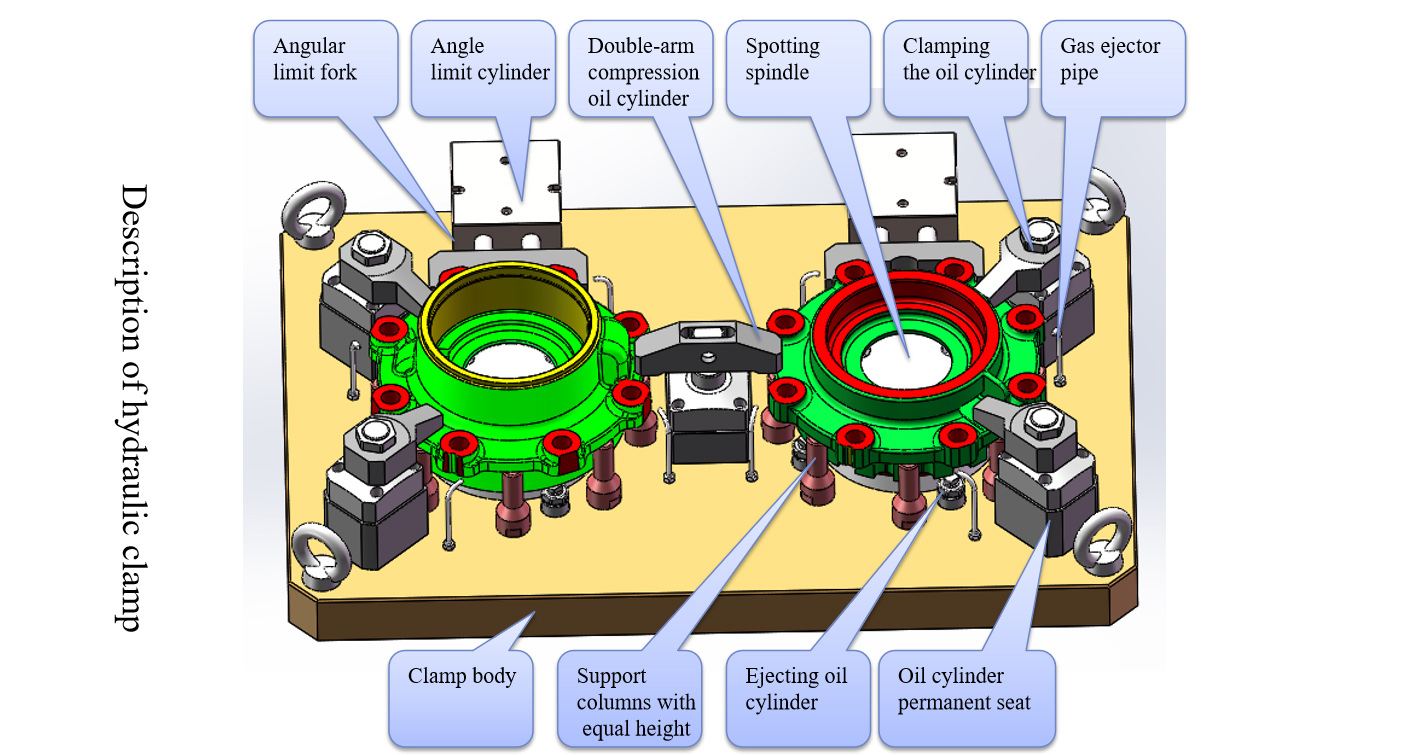
Ausrüstungsanforderungen für die Produktionslinie
1. Die Klemmvorrichtung der Produktionslinienausrüstung verfügt über die Funktionen des automatischen Klemmens und Lösens und realisiert automatische Klemm- und Lösefunktionen unter der Steuerung der Signale des Manipulatorsystems, um mit dem Lade- und Stanzvorgang zusammenzuarbeiten.
2. Die Oberlichtposition oder das automatische Türmodul muss für die Metallplatte der Produktionslinienausrüstung reserviert sein, um mit dem elektrischen Steuersignal und der Manipulatorkommunikation unseres Unternehmens koordiniert zu werden.
3. Die Produktionslinienausrüstung kommuniziert mit dem Manipulator über den Verbindungsmodus eines Schwerlaststeckers (oder Luftfahrtsteckers).
4. Die Ausrüstung der Produktionslinie verfügt über einen internen (Stör-)Raum, der größer ist als der sichere Aktionsbereich der Manipulatorbacken.
5. Die Ausrüstung der Produktionslinie muss sicherstellen, dass sich auf der Positionierungsfläche der Klemme keine Eisenspäne befinden. Bei Bedarf muss die Luftzufuhr zur Reinigung erhöht werden (das Spannfutter muss sich beim Reinigen drehen).
6. Die Ausrüstung der Produktionslinie verfügt über einen guten Spanbruch. Bei Bedarf kann die zusätzliche Hochdruck-Spanbruchvorrichtung unseres Unternehmens hinzugefügt werden.
7. Wenn die Produktionslinienausrüstung einen genauen Stopp der Werkzeugmaschinenspindel erfordert, fügen Sie diese Funktion hinzu und stellen Sie entsprechende elektrische Signale bereit.
Einführung der Vertikaldrehmaschine VTC-W9035
Die NC-Vertikaldrehmaschine VTC-W9035 eignet sich für die Bearbeitung rotierender Teile wie Zahnradrohlinge, Flansche und speziell geformte Schalen. Sie eignet sich besonders für das präzise, arbeitssparende und effiziente Drehen von Teilen wie Scheiben, Naben, Bremsscheiben, Pumpenkörpern, Ventilkörpern und Schalen. Die Werkzeugmaschine bietet die Vorteile einer guten Gesamtsteifigkeit, hohen Präzision, einer hohen Abtragsrate pro Zeiteinheit, einer guten Genauigkeitserhaltung, hohen Zuverlässigkeit, einfacher Wartung usw. sowie eines breiten Anwendungsspektrums. Fließbandproduktion, hohe Effizienz und niedrige Kosten.
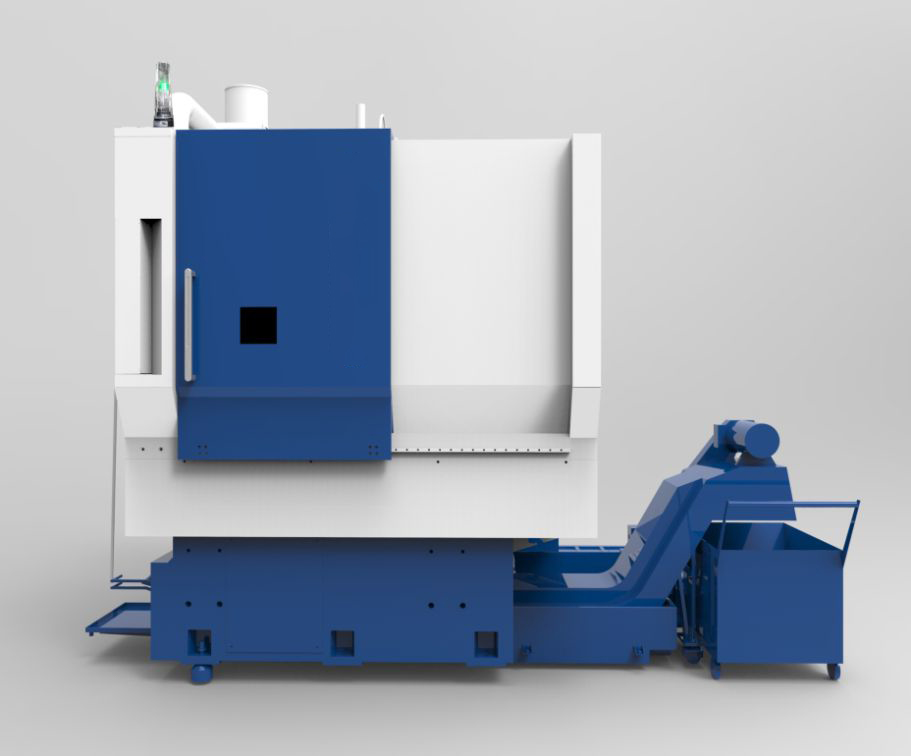
Modelltyp | VTC-W9035 |
Maximaler Drehdurchmesser des Bettkörpers | Φ900 mm |
Maximaler Drehdurchmesser auf der Gleitplatte | Φ590 mm |
Maximaler Drehdurchmesser des Werkstücks | Φ850 mm |
Maximale Drehlänge des Werkstücks | 700 mm |
Drehzahlbereich der Spindel | 20-900 U/min |
System | FANUC 0i - TF |
Maximaler Hub der X/Z-Achse | 600/800 mm |
Schnelle Bewegungsgeschwindigkeit der X/Z-Achse | 20/20 m/min |
Länge, Breite und Höhe der Werkzeugmaschine | 3550*2200*3950 mm |
Projekte | Einheit | Parameter | |
Verarbeitungsbereich | Verfahrweg der X-Achse | mm | 1100 |
Verfahrweg der X-Achse | mm | 610 | |
Verfahrweg der X-Achse | mm | 610 | |
Abstand von der Spindelnase zur Werkbank | mm | 150~760 | |
Werkbank | Größe der Werkbank | mm | 1200×600 |
Maximale Belastung der Werkbank | kg | 1000 | |
T-Nut (Größe × Anzahl × Abstand) | mm | 18×5×100 | |
Fütterung | Schnelle Vorschubgeschwindigkeit der X/Y/Z-Achse | m/min | 36/36/24 |
Spindel | Fahrmodus | Riementyp | |
Spindelkonus | BT40 | ||
Maximale Betriebsgeschwindigkeit | U/min | 8000 | |
Leistung (Nennleistung/Maximum) | KW | 11/18,5 | |
Drehmoment (Nennwert/Maximum) | N·m | 52,5/118 | |
Genauigkeit | Positionierungsgenauigkeit der X-/Y-/Z-Achse (halb geschlossener Regelkreis) | mm | 0,008 (Gesamtlänge) |
Wiederholungsgenauigkeit der X-/Y-/Z-Achse (halb geschlossener Regelkreis) | mm | 0,005 (Gesamtlänge) | |
Werkzeugmagazin | Typ | Scheibe | |
Kapazität des Werkzeugmagazins | 24 | ||
Maximale Werkzeuggröße(Voller Werkzeugdurchmesser/leerer benachbarter Werkzeugdurchmesser/Länge) | mm | Φ78/Φ150/ 300 | |
Maximales Werkzeuggewicht | kg | 8 | |
Verschiedenes | Luftversorgungsdruck | MPa | 0,65 |
Leistungskapazität | KVA | 25 | |
Gesamtabmessungen der Werkzeugmaschine (Länge × Breite × Höhe) | mm | 2900×2800×3200 | |
Gewicht der Werkzeugmaschine | kg | 7000 |
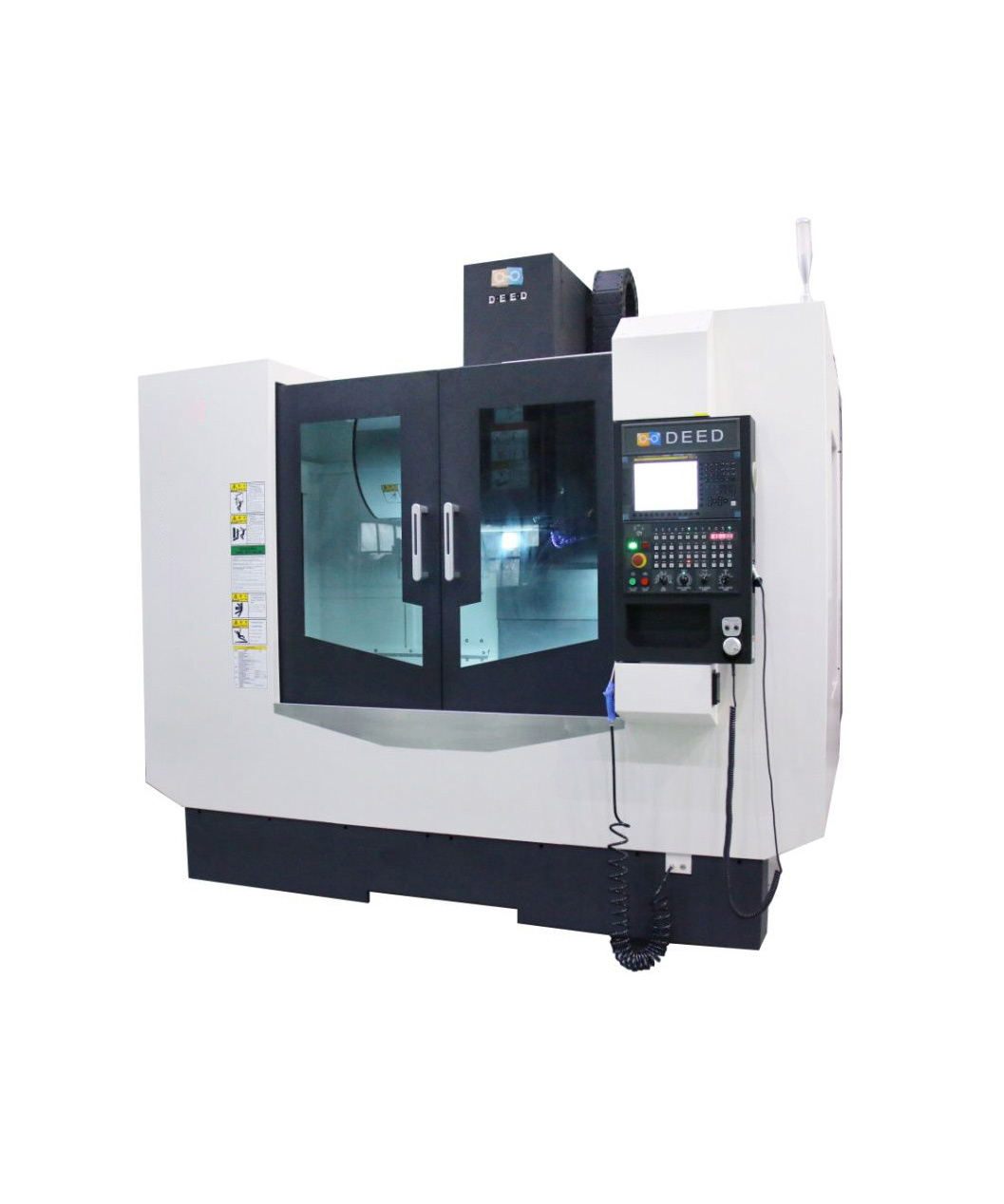